As I did not want to attempt transfers on soft raw clay, my first step was making and curing all the hearts. I made the hearts in layers so they would all have a nice white back to put the logos on. After curing, I sanded them, giving extra attention to the backs so as to have a very smooth surface for the transfers.
![]() | ![]() |
On to the tranfers ... First step is printing your image which is not as easy as it sounds. You want to size the image right to fit your project, and, you want to fit as many images on one sheet of paper as you can as the paper for this is not cheap. I used Avery Light Fabric Transfers paper. Note this paper is designed for use with inkjet printers, which is what most home printers are, so no need to run to a copy shop to use a toner-based printer. My cost was $2 per sheet. Not going to break the bank but not exactly paper you want to waste either. I then used PhotoScape to get about 70 logos per sheet for printing. Took some trial and error there to get the image size and PhotoScape settings just right, but, it's a free program and the best for this purpose of the many I tried. My logo included text, but I printed the image normally. I did NOT make it mirror-image. That reverse-imaging when printing is not necessary with this method.
I cut my sheet into strips and applied a coat of Kato Liquid Polyclay clear medium. (I'm not endorsing PrairieCraft, I have no experience with them, they just had the best product page, LOL)
I had read that you should brush the liquid clay (LC) on in a very thin layer, and do it in two coats, brushing a different direction each time. I found that un-necessary, and, brushing it on very thinly did not work well at all for me. I got much better results brushing it on "normally". In other words, I did not knock myself out trying to get an uber-thin coat, nor did I slop it on thick.
I tried a number of different brushes and got the best results with a somewhat stiff, straight-edged nylon brush. The firm, straight brush and a firm stroke let me apply the LC evenly and smoothed out bubbles at the same time. When brushing on the LC, make sure you cover the entire piece of paper you are working with. Having a straight clean "edge" like that will make peeling the paper backing off much easier. Thus why I cut my sheet of images into strips.

As you can see from the pic, I am very messy when it comes to anything involving a brush so I always work on top of paper I can throw out and replace as often as necessary to keep my work area from becoming a sticky mess.
After applying the LC I baked the strips at 255* for 15 minutes. I placed them on a file folder on a metal cookie tray and used magnets to hold down the ends of each strip, to prevent them from possibly curling up while baking. I also tented the tray with foil. (It took me much trial and error to arrive at a suitable temperature and since ovens all have their own quirks, please experiment on some junk pieces first if you are going to do this, to find the temp that works best for your oven.)
After removing from the oven, I slid them into a pan of ice water. The strips curled up almost immediately upon hitting the water but it's just the paper curling so no matter, it doesn't hurt a thing.

After they are cooled, simply peel the paper backing off.
![]() | ![]() |
Isn't that GREAT? No soaking and scrubbing to remove all traces of paper, it simply peels away!
After I had all my strips baked and peeled, I cut the logos apart and trimmed them. I trimmed very close to the edges of the image as I saw no reason to leave excess LC around them.
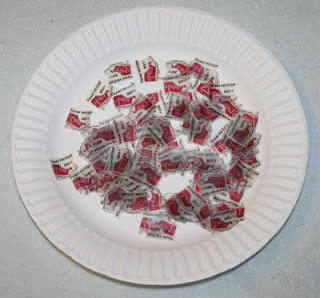
Now I have cured hearts and cured liquid clay transfers. Perfect! This means I do not have to worry about mushing or marring the raw clay piece or smearing the ink or any number of other possible problems that could arise from working on raw clay and wet ink and un-set LC. All I have to do is stick them together. :)
So, using the same brush as above I brushed a very thin coat of LC onto the backs of the transfers. This time, you do want to go as thin as possible, just enough to make the image stick to the surface of your piece. Then stick the transfer, wet side down, onto your piece and press firmly, using your fingers to smooth it from the center out, to make sure you have no bubbles or wrinkles. If you use too much LC, the image will slide around as you press/smooth, so as I said, use just enough LC in this step to make it stick, and be sure to cover the entire back of the image.
With the image in place, I brushed a thin layer of LC over the entire surface. In other words, I covered the entire back of the hearts, not just the image transfer area. I then baked again at 255* for 10 minutes, dunking them in ice water when they came out of the oven.
After cooling, I gave the backs another sanding with 800 then 1000 grit wet/dry paper. One of the best things about this method is that the ink is protected under two layers of LC so it is not going to rub off, or even sand off. (Unless of course you go at it with 60 grit paper or something, LOL.)
At this point, they are done. Finished. Good to go. :) Fully cured and the ink safe under the LC. But, I am obsessed with things being shiny, so I choose to apply a coat of high-gloss glaze to the backs. LC, if a high enough heat is applied to it, will turn shiny and glass-like on its own but that requires great care not to burn or bubble things. Playing with the heat gun is fun, but for a mass-production situation like this, I took the easier/faster way and used the glaze.
And here are my finished pieces (before I applied the glaze):
![]() | ![]() |
Crisp, clear images & text and great color transfer. No scrubbing paper off. No messing with mirror-images. No need to go to a copy shop to make your prints. No worries on the image rubbing off. No worries on mushing the piece out of shape or smearing the ink as you work. Three rounds of baking, yes, but the benefits of this method far outweigh that methinks.
So that's it, that's my method. I read many tutorials on doing image transfers before I embarked on this project and every one was different. I took a little of this and a little of that and experimented until it synthesized into one successful start-to-finish method.
26 comments:
Thanks! That method sounds very do-able.
PrairieCraft is Donna Kato's site, so it is a good, safe place to shop. I buy there all the time.
How very nice of you to treat us to this tutorial. Well done. Thank you so much.
I didn't know that, Gillian. I guess I picked the right site to link to then.
Thankyou, All About Creating! :)
Col, so nice of you to put a free tut out! This sounds like a great one for transfers. I might have to give it a go just for fun!
What a cool toot! You did good. :D xoxoxoxoxoxoxxo
Thanks, Janie! Give it a go. Once I arrived at an overall process that worked for me, it was quite fun and everyone who bought the hearts was like "What? It's all clay? Not a sticker?". Hee!
Thanks, AuntM! I sometimes think I am better at giving directions than following them, LOL.
Very nice and your hearts look excellent! I have read many photo transfer techniques and none of them really impressed me except yours. Well done. I will give it a try sometime and let you know how it comes out. Thanks so much for sharing!
Carolyn
I know nothing about working with clay and I think I could follow these directions. Good job!
Finally got a chance to play with this. Great tutorial and I got perfect results.
Thank you so much!
Thankyou Carolyn, for such a nice compliment! :)
That's terrific Colt! I am thrilled it worked for you. :)
I'm a little late seeing this but it's a great tutorial. Thank you for sharing this.
Thankyou, Bonnie!
have you done this with colored clay? will it leave a "ring" of transfer image around the image?
I haven't done it on colored clay but I imagine it would be fine, perhaps even easier. From past experimenting, doing it on off-white or lighter colors is easier as the color of the clay background "hides" any tint in the liquid clay if it's not totally clear. I would think you could use any color clay though of course the darker the color the less the image will "pop" against the background.
Great tut!!! Very clear and understandable for even a newbie! I've done a similar method of transfer and find this to be the clearest! (I use hp everyday photo paper -50 to a pack- and I do have to soak/rub off the paper.) I'll have to get the one you used now. grin.
Thanks,Pam!
D'you think these transfers could be mounted to something besides clay - like wood or metal? I do gel medium transfers for a lot of projects but currently have a piece that needs clarity, and I have yet to figure out how to remove gel transfers without at least SOME scraped bits...
Gosh, I don't know Aiknami. I know you need to use an adhesive to get polymer clay to stick to metal, and they don't recommend it on wood either because of the possible moisture content I think. But perhaps if you had a glue that would bond the clay to the metal and dry clear, it could work? Come back and let us know if you try it. Thanks for reading!
Could this work with regular printer paper or not?
>> Could this work with regular printer paper or not? <<
Hi Marina,
Yes. I know some people use a technique with regular printer paper but I had zero luck with that and thought scrubbing the paper off was just rotten. You can see the results I got using regular printer paper compared to the Avery transfer paper here : http://colscreations.blogspot.com/2011/01/image-transfer-trials.html
Great tutorial! Would this paper work at the print shop? Or do you know another brand to use on laser printers. I don't have a printer. Thanks again :-)
I know you posted this a few years ago but I just had to say I am SO thankful that you took the time to share this and WOW! Genious!!! I have tried every method I came across...finally had some success with the t-shirt transfer paper but your method has brought it to a whole nother level!!! Thank u so very much and awesome work!!!
Thankyou so much, Abby! I am glad to hear that my older post is still useful. :)
Post a Comment